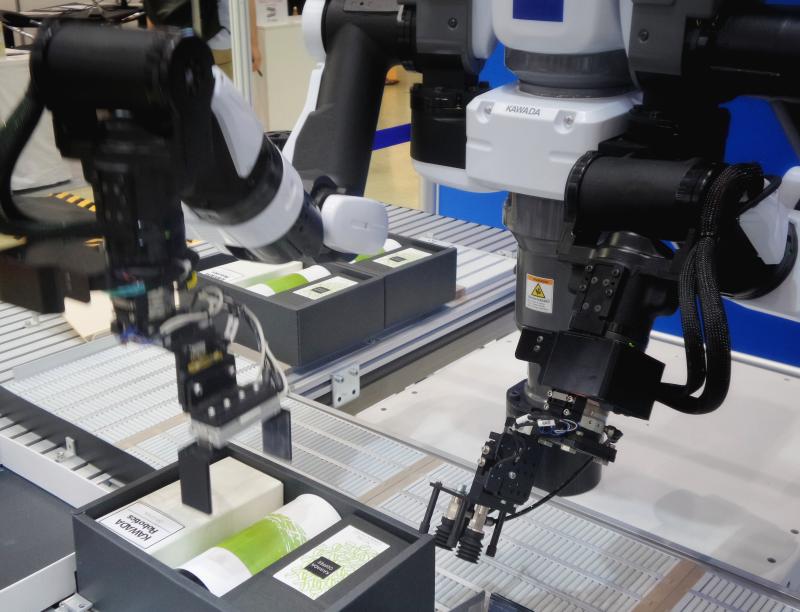
Introducción
En la primera parte de este artículo se concluía indicándose que los modelos de analítica predictiva ofrecen predicciones, pero no decisiones y en el mundo industrial se requieren decisiones. Son los modelos de analítica prescriptiva los que recomiendan las decisiones a tomar, y esto en el mundo industrial, es clave.
En esta segunda parte se describe cómo las nuevas técnicas de analítica prescriptiva basadas en Deep Reinforcement Learning pueden realmente revolucionar el mundo industrial y conseguir sistemas productivos cada vez más flexibles y automáticos.
Retos
Para entender mejor la diferencia entre predicciones y decisiones, veamos un ejemplo.
Para una gestión de stocks (determinar cuántas unidades de cada componente o SKU[1] debemos de tener en nuestro almacén) la analítica predictiva nos ofrecerá una estimación de la demanda futura para cada SKU, pero la decisión a tomar no queda resuelta con la estimación de la demanda. La decisión para tomar debe tener en cuenta muchas otras cosas: cuánto tiempo tarda cada proveedor en enviarnos nuevas SKUs, qué capacidad tiene nuestro almacén para almacenar SKUs, cuánto dinero nos podemos gastar en comprar y almacenar SKUs, qué tasa de SKUs defectuosas podemos tener, etc… Es decir necesitamos resolver un “sudoku”, pero no resolverlo de cualquier forma, necesitamos resolverlo muy rápido y además, que la solución al “sudoku”, sea la mejora posible, por ejemplo en términos de coste para la empresa. Es resumen, necesitamos resolver el problema anterior de forma óptima y este es el mundo de la analítica prescriptiva.
Tendencias
Las técnicas habituales para resolver los problemas de analítica prescriptiva han sido reglas heurísticas (ej. mantener un stock del 5% de la demanda) o técnicas de optimización que son técnicas exactas basadas en programación convexa o aproximadas basadas en algoritmos clásicos de inteligencia artificial (algoritmos genéticos, tabú search, swarm optimization,…). El problema de estas técnicas es que las primeras (heurísticas) aunque son rápidas y fáciles de implementar, las soluciones que ofrecen no son óptimas y por tanto se pierden parte de los beneficios. Mientras las segundas (técnicas de optimización) aunque ofrecen soluciones óptimas o próximas a las óptimas, suelen ser lentas, lo que impide su aplicación en situaciones que requieran tomas de decisiones rápidas, como muchas veces sucede en el ámbito industrial.
Recientemente la unión de una técnica “clásica” de Inteligencia Artificial denominada Aprendizaje por Refuerzo o Reinforcement Learning con las nuevas técnicas de Deep Learning ha dado lugar a unas técnicas muy prometedoras para la industria. Estas técnicas permiten, entrenar un modelo que no busca realizar una predicción sino recomendar una acción. Así en el ejemplo de la gestión de stock el modelo una vez entrenando recomendaría la cantidad de stock mantener de cada SKU, de forma que se minimice el coste. Estas técnicas, que se conocen como Deep Reinforcement Learning (DRL), se pueden entrenar sin necesidad de disponer de ejemplos lo que es una extraordinaria ventaja. Esto se consigue al ir aprendiendo el modelo de forma iterativa mediante prueba y error, recibiendo pequeños “refuerzos” o “recompensas” cuando cuando lo hace bien. Además, es posible realizar este entrenamiento en ambientes simulados lo que es muy adecuado para el mundo industrial ya que minimiza posibles problemas de seguridad o impactos negativos. A continuación, se describen algunos ejemplos:
[1] SKU: Stock Keeping Unit, piezas o componentes que mantenemos en stock
Ejemplos
- Aprendizaje de un robot: utilización de DRL para enseñar a un robot a coger piezas frágiles. El uso de DRL permite entrenar el robot en un ambiente simulado (ambiente virtual), para una vez entrenado transferir el modelo a producción.
- Aprendizaje de montajes complejos: Actualmente los robots se ven limitados en montajes donde existe variabilidad (ej. tamaños de piezas muy variables), mientras los humanos resuelven estas tareas con suma facilidad. Actualmente se trabaja con sistemas DRL siendo el objetivo que los robots aprendan a gestionar la variabilidad de estas tareas complejas de una forma similar a como lo hacen los humanos.
- Recuperación ante fallos graves: El mantenimiento industrial debe estar preparado para una toma de decisiones rápida ante un fallo grave de los sistemas. Actualmente se desarrollan sistemas DRL entrenados en ambiente simulados a partir de los modelos de mantenimiento predictivo, que permiten recomendar acciones para recuperar el sistema. Esto es especialmente relevante cuando estas acciones son muy interdependientes y complejas y/o cuando los tiempos de respuestas deben ser muy rápidos.
- Planificación de operaciones (scheduling): La planificación de operaciones en una planta, consiste en establecer el orden de las operaciones a realizar sobre las piezas en las máquinas (ej. qué pieza debe entrar primero en una máquina) de forma que se cumplan con los objetivos de producción (ej. que los trabajos se entreguen en plazo). Actualmente se está trabajando en el uso de DRL para entrenar modelos off-line y poder aplicarlos on-line con tiempos de respuesta muy rápida. Esto es especialmente indicado en ambientes de trabajo donde se requieren cambios frecuentes de planificación.
Además de lo ya señalado, la Inteligencia Artificial se puede integrar con diferentes tecnologías para dar respuestas a otros retos del mundo industrial. A continuación, se describen tres ejemplos:
- Realidad Aumentada para la mejora de la productividad: La realidad aumentada se está utilizando para ayudar al operario en distintos procesos con vistas a aumentar su productividad. Por ejemplo, el uso de gafas de realidad aumentada y modelos de IA, permiten al usuario visualizar la pieza real y superpuesta sobre ella instrucciones de montaje o alertas en caso de error de montaje.
- Procesamiento del lenguaje natural (Texto): Continúan existiendo áreas no digitalizadas (partes de trabajo sobre papel) o donde los datos están poco estructurados (ej. documentos en formato pdf). En estos casos es necesario “estructurar” estos datos para que puedan ser utilizados. Por ejemplo, una empresa recibe informes en formato PDF de resultados de inspecciones de calidad (ej. análisis de rayos X de soldaduras) de diversos laboratorios y necesita volcarlos en su ERP (Enterprise Resource Planning o sistema de planificación de recursos empresariales). Esta tarea conocida como “extracción de información” requiere de modelos de IA dentro de un área denominada NLP (Procesamiento del Lenguaje Natural o Natural Language Processing), que sean capaces de “extraer” los datos de interés (número de la pieza, nombre del inspector, resultados de la inspección,…) de los distintos PDFs y volcarlos de forma estructurada a una base de datos (ej. a un ERP).
- Procesamiento del lenguaje natural (voz): La voz es la forma natural de interacción de los humanos, los avances en esta área del Procesamiento del Lenguaje Natural, permite una comunicación cada vez más fluida entre personas y sistemas a través de la voz, siendo esto muy útil en ambientes industriales donde el operario tiene las manos ocupadas (o con guantes) o donde el esfuerzo de interacción manual con una consola puede restarle productividad.
Conclusión
Como conclusión, podemos decir que la Inteligencia Artificial, debe permitir superar las limitaciones actuales de la automatización, principalmente su falta de flexibilidad y aquí las nuevas técnicas de DRL pueden ser claves. Pero también, poner en valor datos pocos estructurados como imágenes, voz, texto,…, mediante nuevas funcionalidades basadas en la explotación de dichos datos, así como interacciones mucho más naturales entre los operadores humanos y los sistemas industriales.