
El mantenimiento de activos industriales es un tema recurrente donde la tecnología y, en concreto la IA, juegan un papel relevante hoy en día. Se estima que las empresas dedican en torno al 5% de sus ingresos a mantener sus plantas, vehículos, instalaciones y maquinaria. Adicionalmente, tienen que hacer frente a costes adicionales no previstos por fallos, roturas o paradas inesperadas de estos activos, que pueden suponer lucro cesante, pérdida de clientes, impacto en la imagen; por no hablar de los riesgos para la vida o salud de los operarios.
La digitalización progresiva del proceso y con ella la llegada de nuevos datos, facilita la transición de un mantenimiento reactivo a otro proactivo e inteligente, en el que los operadores cuentan con herramientas que les permiten no limitarse a corregir problemas sino a prevenirlos y, más aún, predecirlos.
En este artículo exploramos las soluciones tecnológicas que están apareciendo en el mercado para realizar un mantenimiento inteligente de estructuras estáticas como pueden ser plataformas de extracción, aerogeneradores, grúas, puentes o tanques, poniendo foco en aquellas instaladas en el mar (offshore); si bien aplica a cualquier activo sujeto a las inclemencias de la climatología, el envejecimiento, el desgaste, la fatiga de los materiales y en general las consecuencias del uso y el paso del tiempo.
Existen herramientas que pueden orientar sobre dónde priorizar las inspecciones rutinarias, qué zonas hay que reparar o mantener, qué evolución puede tener una degradación o corrosión identificada para evaluar los riesgos y estimar el impacto económico de la situación del activo a lo largo del tiempo y en el futuro.
El reto de optimizar el mantenimiento de estructuras en el mar
El objetivo final de todo mantenimiento es minimizar los riesgos (de parada, degradación o fallo) con el mínimo coste. Los recursos económicos (personal, tiempo, herramientas) son limitados. Con los recursos que hay, se debe maximizar la vida útil, mejorar los tiempos de parada y reducir los riesgos de una manera óptima.
En el caso de estructuras estáticas los problemas que queremos prevenir son principalmente los relacionados con la corrosión (como el óxido), roturas, picaduras, abolladuras, deformaciones o perforaciones.
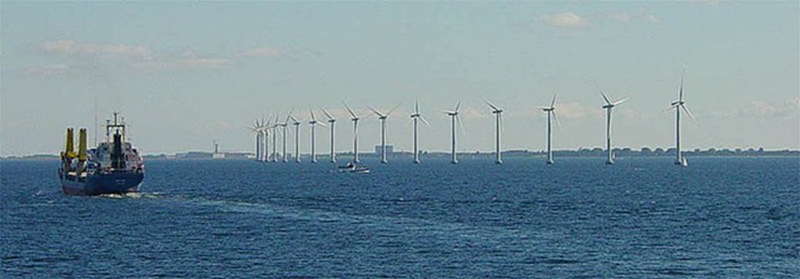
Cuando además estas estructuras están funcionando en el mar (como los parques eólicos offshore), a la propia operación de las estructuras se le añade el impacto del agua salada, el oleaje y la inestabilidad del terreno, con la consiguiente dificultad y enorme coste de realizar mantenimientos en un entorno eminentemente hostil.
Parece obvio que en esta situación es todavía más importante un mantenimiento inteligente. Pero, ¿cómo podemos optimizar el mantenimiento a realizar en estas condiciones?
Historia y tendencias: Inspección y mantenimiento
Tradicionalmente, el mantenimiento periódico programado junto con la inspección visual rutinaria y cíclica han sido los métodos más utilizados de cara a mantener un estado de salud adecuado para los materiales. Así mismo, información sobre reposiciones o corrección de defectos suele recopilarse en formularios en papel, perdiendo la posibilidad de mantener un histórico del mantenimiento llevado a cabo. La consecuencia es que expone al activo a riesgos innecesarios, puesto que sólo se reacciona por el paso del tiempo o si se detecta (con suerte) una anomalía en un momento determinado.
Un paso adicional a este enfoque manual consiste en la utilización de herramientas de ingeniería que permitan evaluar de manera matemática la degradación esperada y la evolución de los materiales. Estas herramientas, sin embargo, están habitualmente únicamente a disposición de los ingenieros de diseño del activo, y se utilizan por los fabricantes del mismo pero no llegan a aplicarse en la fase de mantenimiento a pesar de tener un mayor recorrido (entre 20 y 50 años) y suponer un coste financiero mayor que la propia adquisición del activo.
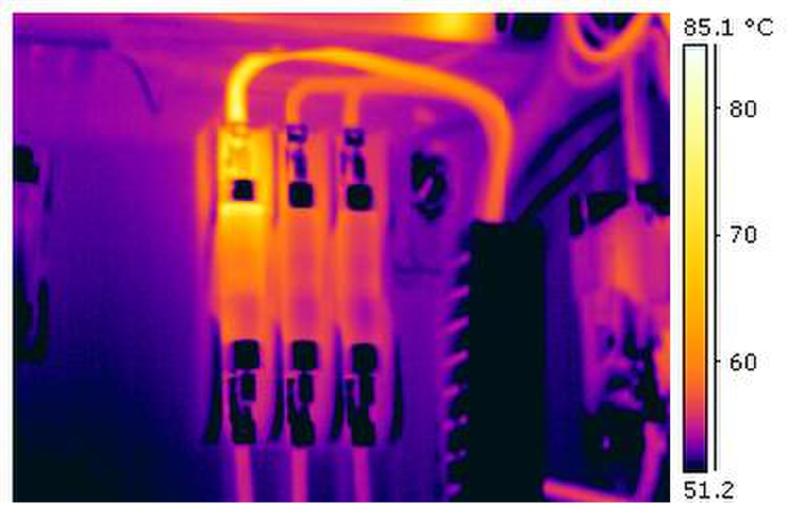
En la última década se ha empezado a prestar importancia a digitalizar la fase de mantenimiento, normalmente conectando varias herramientas que permiten llevar un control de los datos de esta etapa, recopilando digitalmente los datos de inspección y estado del activo, bien mediante introducción manual de datos en una aplicación o la automatización del envío de datos desde sensores, herramientas de inspección o auditoría (como termógrafos) o incluso drones que realizan una recopilación de imágenes del activo.
La conexión de todas estas herramientas lleva a comenzar el camino de la creación de un gemelo digital del activo en operación y su historia de mantenimiento, abriendo la puerta a un sinfín de aplicaciones, especialmente si logramos que sea inteligente.
Métodos analíticos de optimización de mantenimiento
Para poder realizar un mantenimiento inteligente, optimizado, que realmente minimice los riesgos con relación al gasto que es posible realizar, necesitamos disponer de datos, cuantos más mejor, gestionados por nuestras herramientas digitales en un digital flow continuo y con garantías de calidad. Información que pueda ser consultada, visualizada, manipulada por los ingenieros, llegándose a conseguir reducciones en los gastos de mantenimiento de entre un 10% y un 40%.
Son herramientas estadísticas y analíticas, que combinan modelos matemáticos con machine learning para obtener una serie de conclusiones de los históricos de datos:
- Análisis de la integridad de la estructura, visualizando con un código de colores el estado evaluado de cada parte de la estructura estática, con la granularidad y detalle necesario, pudiendo navegar por los activos en 3D
- Seguimiento de la corrosión, produciendo curvas de salud que muestran la degradación esperada, ayudando en las decisiones de sustitución o reparación, permitiendo aplicar modelos estadísticos y matemáticos probados
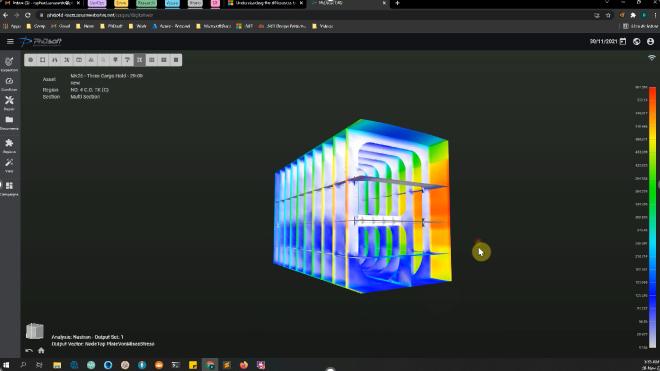
Evaluación según estándares de la industria, como por ejemplo las normas de Fitness for Service (FFS o EAS en castellano) del tipo de la API 579, que permite realizar análisis de la pérdida de metal, picaduras por corrosión, ruptura por fragilidad, etc.
En el caso de los activos en el mar, por ejemplo, los nuevos parques de aerogeneración offshore que están ganando popularidad, las herramientas disponen de modelos específicos y muy necesarios para este nuevo tipo de entornos:
- Modelos Hidrodinámicos, que evalúan el efecto del oleaje y las fuerzas del mar sobre la estructura estática de plataformas y pies de los aerogeneradores.
- Modelos de Análisis de Elementos Finitos, que analizan las estructuras para evaluar su aptitud para el servicio.
- Modelos de anclaje (mooring) que analizan la salud de los amarres con el terreno y su evolución en el tiempo.
- Modelos de estabilidad para comprender los riesgos de colapso o hundimiento de estas estructuras sometidas a fuerzas que pueden llegar a ser muy importantes según la climatología.
Se cuenta así con nuevas herramientas que complementan la labor de los ingenieros de mantenimiento, que ven aumentadas sus capacidades, permitiéndoles tomar decisiones, priorizar trabajos, evaluar su instalación basándose en información completa, fiable y analizada. La operación así entendida está permitiendo a las empresas diferenciarse en el competitivo mercado de las grandes estructuras industriales en el mar.